半導体メーカーF社 開発製造部
デバイスを提供する上で、最も重要なことは信頼性…
検査工程の静電気放電を大幅に低減し、納入先にも認められた樹脂材料とは
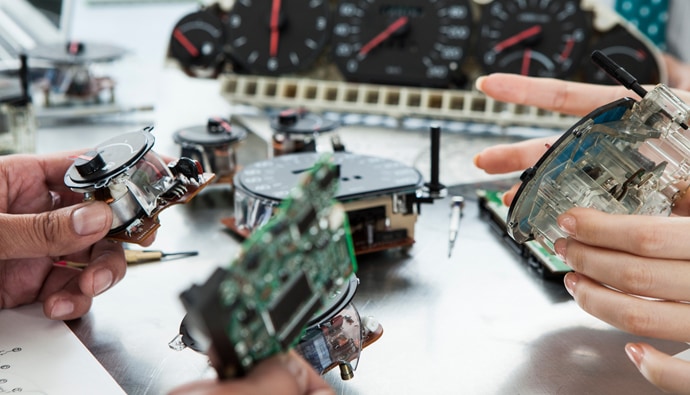
背景
半導体メーカーのF社は、納入先である自動車メーカーからの要求で、静電気放電(ESD)対策の見直しに迫られていた。自動運転の制御に使用する半導体デバイスの短寿命の原因となるESDによるダメージを徹底的に排除したいという要求をクリアすべく、対策は万全を期していたが、あらためて工程を観察することにした。
課題
テストハンドラで静電気放電が発生。剥離帯電、摩擦帯電を抑制しなければ…
自動車に搭載される電子機器の高機能化に伴い、車載用半導体製品には、今まで以上に高い品質レベルが求められています。今回、納入先である自動車メーカーよりESD対策を見直すよう要求があり、開発製造部門のT氏は、次のように話します。
「自動運転システム向けデバイスを提供する上で、最も重要なことは信頼性です。信頼される品質を実現するためには、定期的な工程管理の見直しや機能安全への対応などを通じて、より良い製品提供に努める必要があります。」(T氏)
もともと接地をとる、イオナイザーを使用するなど、電荷の蓄積を防ぐ対策には万全を期していましたが、あらためて検査工程を観察してみることにしました。すると、最終工程で使用するテストハンドラで、わずかながら静電気放電が発生していることが発覚したのです。調査を進めると、デバイスとソケットの間で剥離帯電、そして搬送に関わるマガジンやガイドレールで摩擦帯電が原因となっている可能性が考えられました。
工程内の静電気放電による故障に至らないダメージでも、出荷後の故障原因となり製品寿命が短くなったりするリスクがあります。近年の高集積化・微細化に伴い、ESDダメージのリスクはますます大きくなっており、高性能な半導体製品ほど静電気耐性が低下する恐れがあることから、早急な対策が必要でした。
現在の対策に改善の余地があることから、T氏はハンドラ構成部品の材料から見直すべきだと判断し、適切なソリューションを見つけるべく動き出しました。
課題のポイント
-
故障に至らない静電気放電でも、目に見えないダメージが回路に発生し将来の故障原因になることがある
-
テストハンドラで発生する可能性のある剥離帯電、摩擦帯電による放電を抑制する必要があった
-
放電を防ぐため、ハンドラ構成部品材料の見直しが急務